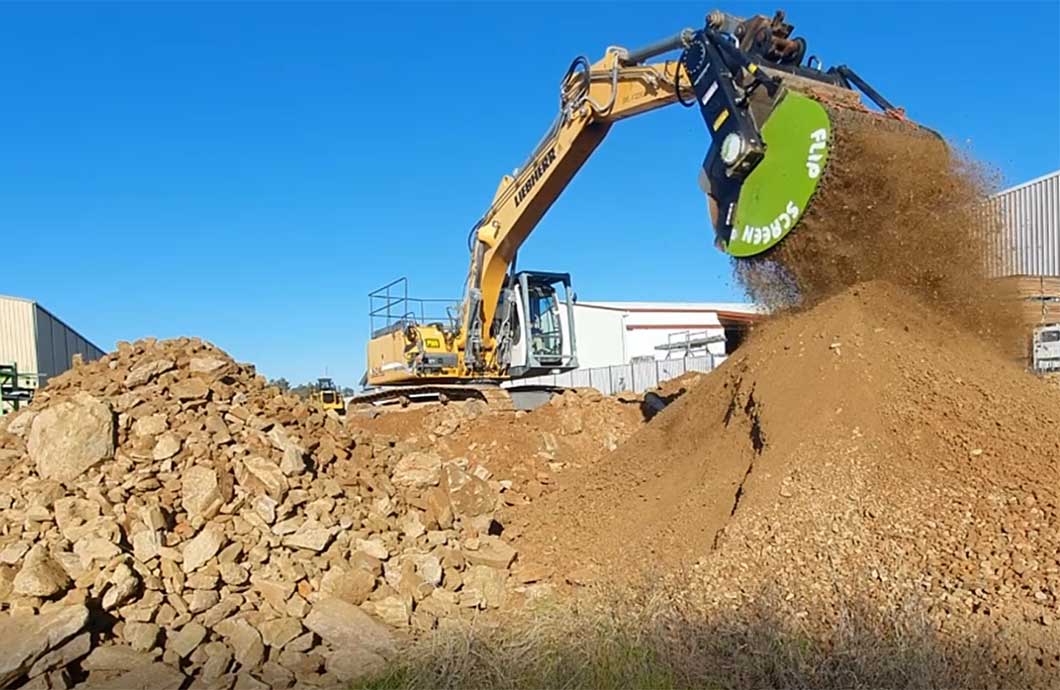
There is a trend emerging as well as a heated debate to go along with it. People on either side argue the pros and cons, with more and more deciding to replace trommel screens of any size or opt instead to purchase more mobile attachments, namely, the FlipScreen.
The conversation ultimately comes down to costs. Which costs more and which will provide greater profits. There are, however, many more points, that certainly warrant mentioning.
FlipScreen has weighed in with their talking points, so let's dive in... a FlipScreen is a portion of the cost of a Trommel screen. Not to mention much lower operating costs, maintenance, etc. Furthermore, the FlipScreen can screen more than a trommel, which means you pay it off sooner and are then making pure profits for much longer!
The screen size of a Flipscreen is hard to gauge with it being rolled, but it is bigger than one assumes. Sometimes even bigger than that of a trommel, depending on the carrier it has been designed for. You also screen the material once, where it is, or straight into a truck, rather than having to take the material to the screener, allowing you to spend more time screening, rather than traveling to and from where the material needs to be screened. This is a big saving on time for screening, which means more material screened per hour. Another major advantage is the reduced capital and labour expenditure required to run a screening operation utilising FlipScreens. Rather than having 2 loaders, or 2 excavators preparing the site for a trommel screen, put some FlipScreens on them and they dig, and screen at the same time.
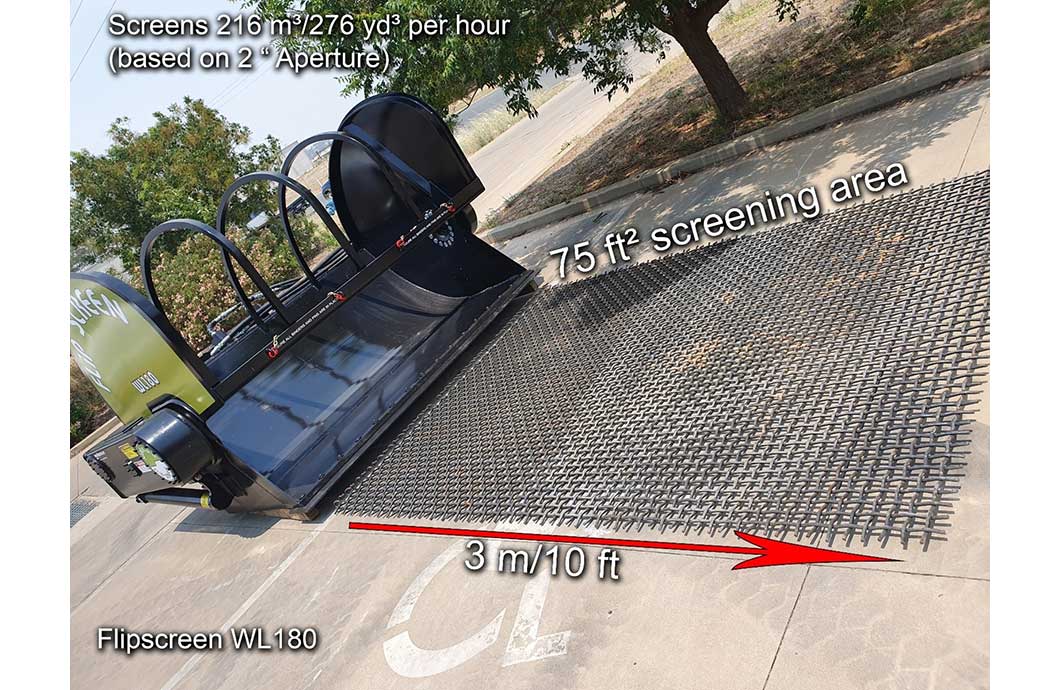
Moving on from screening rates, lets discuss material. A FlipScreen is capable of screening ANY material. It can be used underwater, with corrosive materials and to dig fresh ground. A trommel on the other hand, cannot process many materials easily, and has significant problems with certain types. For example, hot Charcoal and scrap metal are both known to ruin trommel belts.
Quite often when a material differs in moisture or content, you will find a lot of unscreened material will go straight through a trommel as it has run out of screening area. In this case the material has to be scooped off “the finished pile” and refed through the trommel. On a FlipScreen, the operator has total control over when the material is sufficiently screened. If the material is wet or difficult, the operator simply does a couple of extra rotations and the job is done. Once and properly!
It is mentioned a lot, how much "time" is wasted when using a trommel. It is a common thing to weigh up whether or not a stockpile justifies the time it takes and set up costs of a “portable” trommel. While portable trommels are called “portable”, we all know that by the time you set up a pad, unfold and get the trommel started, it is usually a one day job. Whereas the FlipScreen, attaches to machines which are already on site. Set up time is eliminated with a FlipScreen, and with far less complex site requirements and moving machinery, it is far easier to manage. You also don’t have to worry about even ground, which is a big concern on many sites for a trommel or portable screening plant.
To change the mesh size on a trommel requires removing, paying for and replacing the whole barrel; where as with a FlipScreen the mesh change takes 5 minutes without tools at a very low cost.
There are also lower personnel requirements. One operator for one carrier machine and your site is operational. No need for multiple people to pay and manage.
In the world of logistics, you want things to be simple, and transporting one carrier machine saves on money, time, and complexity. The FlipScreen can be changed between carrier machines with very little hassle. A FlipScreen can even be floated on a truck still attached to the carrier.
Between sites and on-site, moving a FlipScreen is a dream, whereas moving a trommel screen is a nightmare.
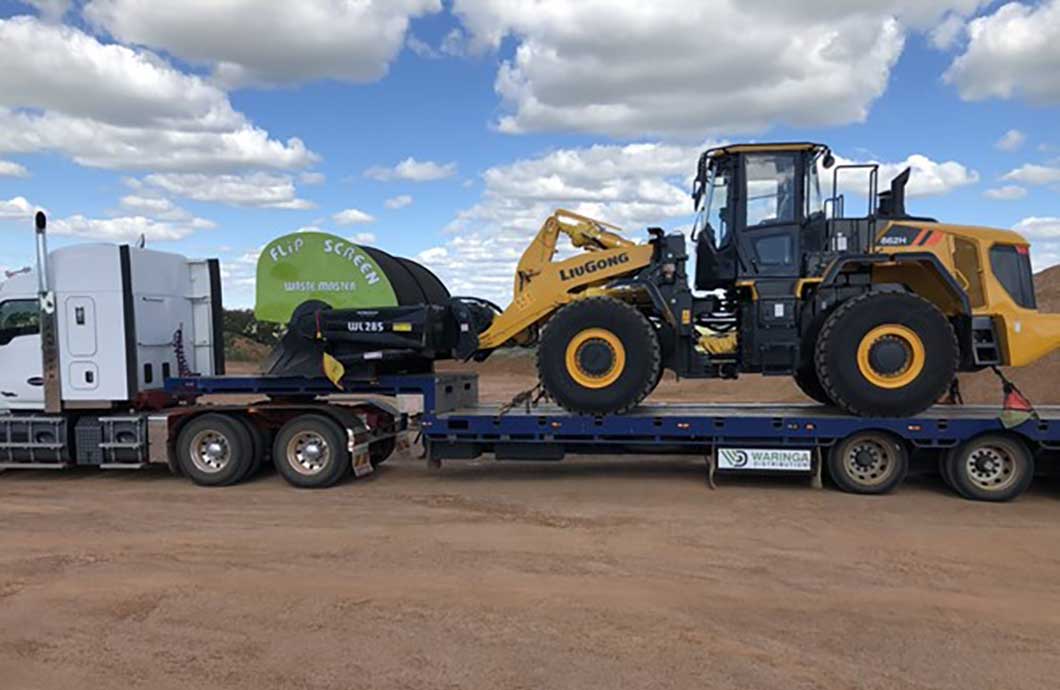
Direct drive Flipscreen models do not require daily maintenance. They are non-vibratory and have no internal moving parts. FlipScreen calculates maintenance costs on the EX85 DD and EX145 DD models to be around 2 cents per hour. Directly compared to a trommel screen, this is another area where the FlipScreen revolutionizes screening.
The FlipScreen on one carrier machine also takes up minimal space for sites that require the economy without any impact on results. Construction sites are especially sensitive to size constraints, which suits FlipScreen perfectly.
Screening more material, with less machinery, less personnel, less time, less upfront expenditure, and ongoing expenses, all relate to greater profits.
In conclusion, we see many arguments, that lead to financial sense in picking a FlipScreen over a trommel screen.
It’s a radical shift in mindset. You need to think differently to achieve more, but the proof is in the profits.
Let us know your thoughts and to find out more about the FlipScreen: https://www.flipscreenglobal.com/my-machine/skid-steer-screening-bucket/.