Imagine stumbling upon a vintage 1970s bulldozer.
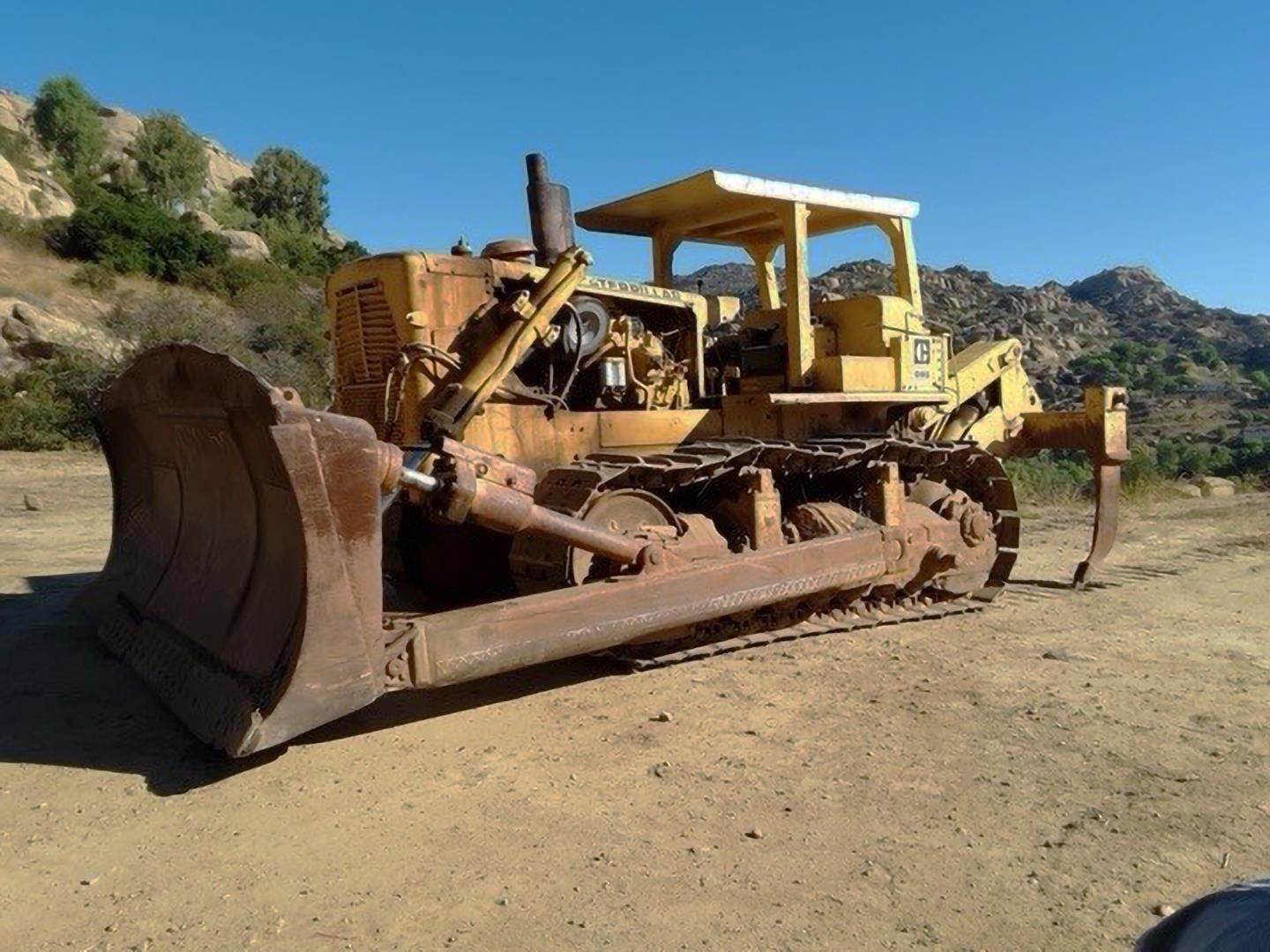
Its once vibrant yellow paint has faded, and the metal shows signs of wear and rust. Yet, its engine hums to life with a promising roar, hinting at the potential for revival. This bulldozer isn't just a piece of outdated machinery; it's a testament to durability and engineering.
Now, imagine transforming this outdated equipment with modern upgrades that boost its efficiency, safety, and environmental compliance.
This scenario is not just a dream for many in the construction industry—it's a viable business opportunity and a sustainable choice with numerous benefits.
However, navigating the legalities and best practices of refurbishing and modifying used construction equipment requires knowledge and care.
This article is your guide to understanding the intricacies of upgrading used construction equipment legally and safely. Whether you're a dealership, a private seller, a potential buyer, or an operator, knowing the dos and don'ts can help ensure that your investments are sound, compliant, and beneficial in the long run.
Table of Contents
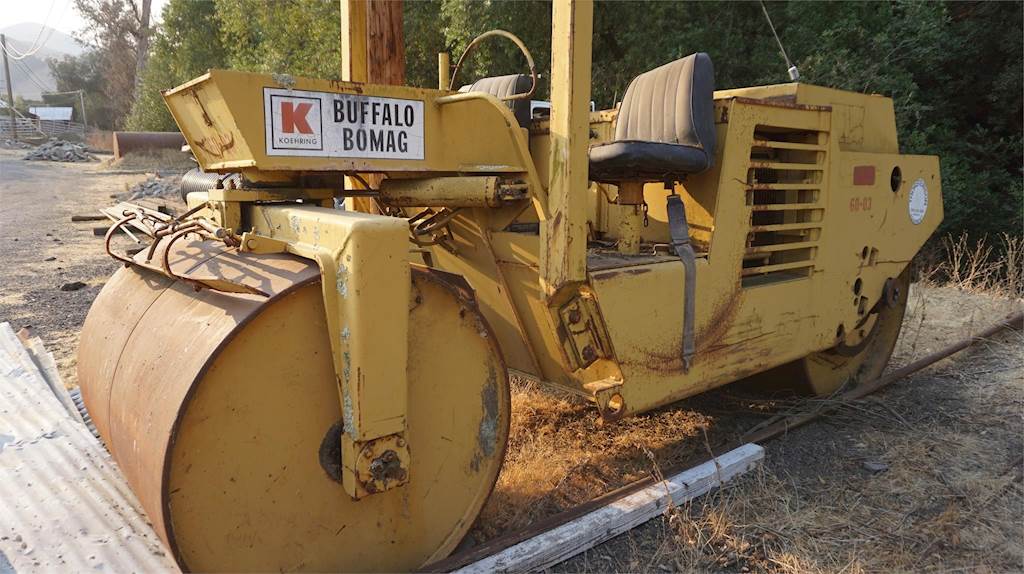
1973 Koehring S812 Smooth Drum Rollers
Upgrading used construction equipment is not just about making old outdated machinery look new. It involves ensuring that the equipment meets current safety and environmental standards.
Regulations can vary significantly from one region to another, but there are generally recognized standards and certifications that equipment must meet—such as those set by the Occupational Safety and Health Administration (OSHA) in the United States and similar bodies worldwide.
These laws often require that modifications do not compromise the machine's safety and that any emissions meet current standards.
To give us an understanding, let's take a look at a few examples of different regulations about equipment modification of cranes and derricks from OSHA (Occupational Safety and Health Administration)—along with rephrasings of the regulations and real-world scenario examples where they would be applied.
OSHA Regulation 1926.1434(a)
Modifications or additions that impact the equipment's capacity or safety are allowed only under specific conditions.
Translation: You can't just change or add something to your heavy equipment without following the rules. This ensures the changes don't make the equipment unsafe.
Example: A construction company wants to add a new attachment to their crane that increases its lifting capacity. They must follow OSHA's specific conditions to ensure it's safe to use.
Manufacturer's Approval Required (1926.1434(a)(1))
The equipment manufacturer must approve any modifications in writing, ensuring updates are made to relevant documents and the original safety factor isn't reduced.
Translation: If you want to modify your equipment, the maker of that equipment has to say it's okay in writing, and you might need to update the equipment's manual or labels to reflect the changes.
Example: Before adding a more powerful engine to a forklift, the company obtains written approval from the forklift's manufacturer and updates the operating manual accordingly.
Manufacturer Refusal or Non-response (1926.1434(a)(2))
If the manufacturer refuses to review the modification or doesn't respond within 30 days, a qualified engineer can approve the modification, maintaining safety standards.
Translation: If the equipment's manufacturer ignores your request or says no without checking the details, a certified engineer can step in to approve your changes, as long as it's still safe.
Example: A company wants to modify its bulldozer for a special project, but the manufacturer won't respond. A registered engineer reviews and approves the modification instead.
Unavailable Manufacturer (1926.1434(a)(3))
This rule applies when the manufacturer cannot be contacted or is no longer in business, allowing for engineer approval of modifications.
Translation: If you can't get in touch with the equipment manufacturer because they're out of business, you can have an engineer approve your modification.
Example: A landscaping business needs to modify an old excavator, but the manufacturer has closed down. An engineer approves the changes, ensuring they're safe.
Review Delay (1926.1434(a)(4))
If the manufacturer doesn't complete a review within 120 days, modifications can proceed with engineer approval.
Translation: If the manufacturer takes too long (over 4 months) to check your proposed changes, you can go ahead with an engineer's approval.
Example: An energy company's request to upgrade its crane is stalled by the manufacturer. After four months without a decision, an engineer steps in to approve the upgrade.
Equipment with Multiple Manufacturers (1926.1434(a)(5))
For equipment used in marine sites with parts from different makers, the modification process follows the same rules as manufacturer refusal.
Translation: If your marine equipment has parts from various brands, you treat it like the manufacturer didn't respond when you want to make changes.
Example: A marine construction firm needs to modify a barge with components from several manufacturers. They follow the procedure for when a manufacturer refuses to review.
Manufacturer's Technical Safety Rejection (1926.1434(b))
Modifications rejected by the manufacturer for safety reasons must not proceed unless the rejection is not explained in writing.
Translation: If the maker of your equipment says no to a change because it's unsafe, you have to listen unless they don't tell you why in writing.
Example: A transport company's proposal to modify their trucks is rejected by the manufacturer for safety concerns. The company cannot proceed with the modifications.
Military Modifications Exemption (1926.1434(c))
Modifications approved by the U.S. military are not subject to these regulations.
Translation: The military has their own approval process.
Example: A defense contractor modifies military vehicles with new armor plating approved by the military, bypassing the usual approval process.
Keep in mind that these above-listed regulations are not intended to act as a summary of all construction equipment regulations concerning upgrades.
For more examples of regulations about equipment upgrading, here is a list of helpful resources:
- United States:
- Canada:
- European Union:
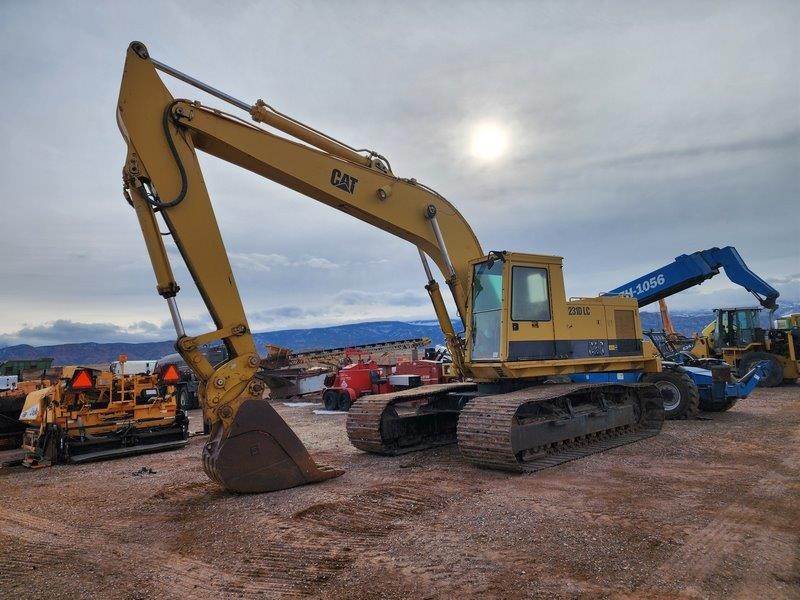
1990 Caterpillar 231 Excavator
Ensuring compliance starts with understanding the specific regulations that apply to your equipment and the region it will operate in.
This might involve consulting with regulatory bodies or hiring experts in equipment compliance.
Documentation is key—maintaining detailed records of all modifications can help prove compliance in case of inspections. Additionally, using certified parts and adhering to manufacturer guidelines can further ensure that upgrades meet legal standards.
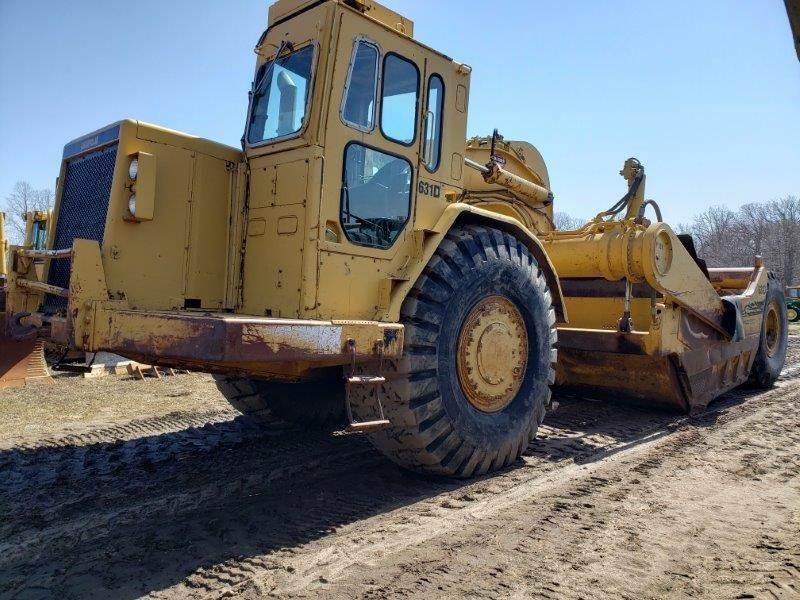
1984 Caterpillar 631D Scraper
Conducting Thorough Inspections
Sometimes, older equipment may not be able to handle necessary upgrades—either in terms of weight, torque, or dimensions. Before any work begins, identify any issues that could be exacerbated by upgrades.
Prioritizing Essential Upgrades
When brainstorming an upgrades list, start in order of which are the most valuable and important. Upgrades that improve safety or reduce emissions should take precedence over cosmetic changes.
Working with Reputable Suppliers
Not all parts are created equal. For a successful upgrade, ensure that parts and components are reliable and certified.
Making Unauthorized Modifications
Unauthorized modifications can void warranties or violate regulations, so they should be avoided at all costs.
Overlooking the Impact of Modifications
Many upgrades will drastically change how a piece of equipment performs—impacting the equipment's balance, structural integrity, or operational capabilities. Make sure that you are prepared to handle all changes that an upgrade brings.
Ignoring the Need for Professional Assessments and Installations
Just because you've identified what work should be done, you can't just start replacing parts willy-nilly—you need the help of professionals. Failing to seek the help of professionals for installations and assessments can lead to safety hazards.
Cost Savings
As a buyer, buying used upgraded equipment tends to be more affordable in comparison to buying new equipment.
Environmental Sustainability
Even though opting for a new, more environmentally friendly piece of equipment greatly decrease your carbon footprint, extending the life of existing machinery means reducing the waste of sending older-yet-still-functional machines to the rust heap prematurely.
Improved Efficiency and Safety
If you're not upgrading to new equipment models, upgrading the equipment itself can go a long way in making projects more profitable and workplaces safer.
Upgrading Breathes New Life into Older Equipment
Upgrading used construction equipment is a viable way to breathe new life into older machines, ensuring they are safe, efficient, and compliant with current standards. It's a journey that requires diligence, knowledge, and a commitment to quality.
For those looking to buy or sell upgraded used construction equipment, My Little Salesman has your back with a vast selection of heavy equipment listings. You're invited to find or list any used equipment for sale today to keep old timers on the job—equipment pieces, that is!
Find Quality Used Construction Equipment for Sale Today