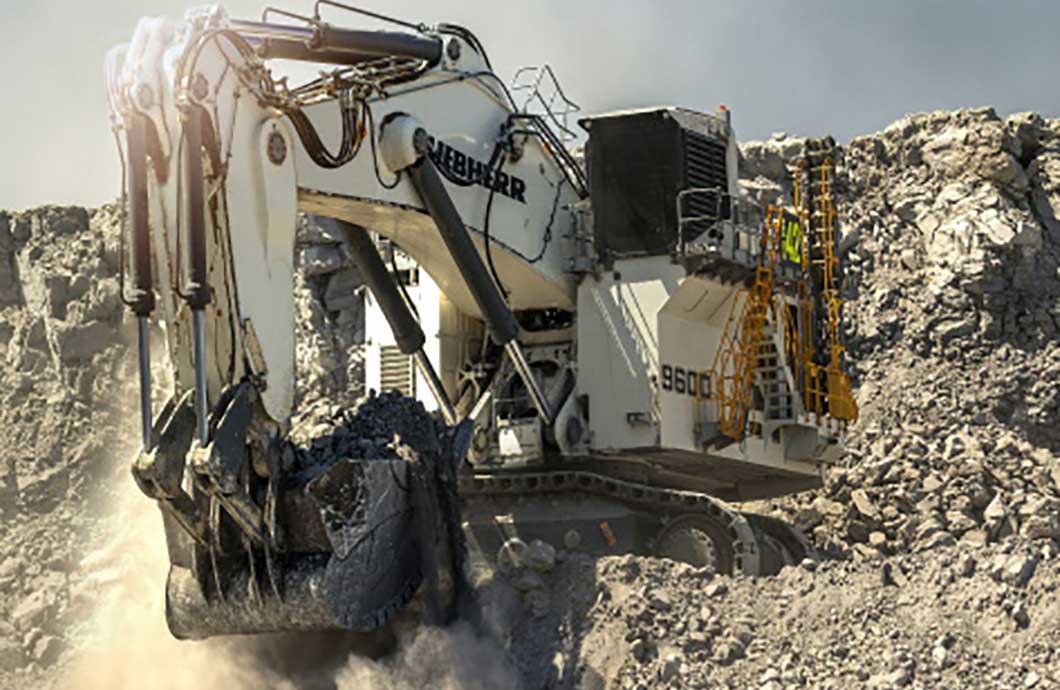
After years of development, the Mining Division of the Liebherr Group is proud to launch the new R 9600 hydraulic excavator. This 600t excavator sets new standards in the open pit mining market.
The successor of the popular R 996B enters the market after gaining a year of field experience in Australia, the largest market for 600-tonne class excavators. This new development builds on years of customer-centric research and is based upon the successful R 9800 800-tonne excavator. A total of 8 units will be operating in Australia by end of 2021. The R 9600 will enter serial production at the end of this year.
A customer-centric approach
Customer input has played an important and pivotal role in the development of this new machine. Engineering, sales and marketing teams have collected feedback and insights from mine site equipment operators, maintenance personnel and procurement groups as well as executive management to have a clear understanding of the challenges they meet every day. The new R 9600 aims to reach the highest standard in terms of safety, sustainability, performance, lifetime, Total Cost of Ownership (TCO), ease of maintenance and more.
After testing the first prototypes at the factory proving grounds in Colmar, France, in early 2020 the first R 9600 pre-series excavators started operating in iron ore and coal applications in Australia. Liebherr, together with its two very important customers BHP and Thiess, started the partnered validation of the first two units in the field. Backed by this succesful validation phase, the R 9600 is ready to enter the global market.
Diverse offering of powertrains including electric drive
The R 9600 is equipped with two QSK50 Cummins engines with advanced combustion technologies. Understanding that fuel costs form the major portion of the TCO for mining machines, Liebherr has developed and implemented LPE solutions (Liebherr Power Efficiency). These proprietary management systems for the engine and hydraulic system controls substancially reduce fuel consumption without compromising the overall productivity of the machine. These new features grant also an additional step toward the Liebherr emission reduction solutions.
For emission regulated regions, a US EPA Tier 4f / EU Stage V compliant version is available with the latest SCR after-treatment technology. Complying with stringent emission regulations, the SCR system reduces nitrogen oxides by injecting a liquid reductant into the exhaust stream.
An electric drive version will be available soon, a productive choice for mine sites having the required electrical infrastructure.
Weight-optimized attachment
The R 9600 attachment makes use of smart component design such as the patented “EVO” backhoe bucket, hydraulic cylinders, shift levers, bucket links and attachment pins. The result is an increased overall production rate without compromising component lifetime.
In standard backhoe configuration with a Heavy Duty wear package, the R 9600 comes with a 37.5 m3 / 49.1 yd3 bucket to deliver an ideal truck/shovel match with Liebherr mining trucks. It loads 190t trucks in 3 passes, T 264 240t trucks in 4 passes, T 274 300t trucks in 5 passes and T 284 375t trucks in 6 passes.
The excavator is also available in face shovel configuration equipped with a 37.0 m3 / 48.4 yd3 shovel, as standard with a Heavy Duty wear package.
Long-lasting performance
Designed to be used in all applications globally, the R 9600 is built to last over 80,000 machine operational hours. Further improving machine reliability, the uppercarriage structure is a completely new development. The robust undercarriage with a fatigue resistant steel structure, is enhanced with a new hydraulic track tensioning system. The standard sealed for life heavy-duty carrier and track rollers incorporate the patented roller path design and registered track pad design.
As an Original Equipment Manufacturer (OEM), Liebherr has built a solid reputation in the development and production of high quality components for mining applications. The R 9600 benefits from this reputation through reliable components that are developed and manufactured by Liebherr. The R 9600 utilizes the latest quality control systems to ensure the best reliability and highest performance.
The latest cabin generation
The R 9600 has a brand-new cabin designed by operators for operators – it is a first-class, state of the art 14 m3 / 150 ft3 working space. The cab design reduces vibrations and limits noise to 69 dB, providing a comfortable working environment for the operator.
To allow for the best possible working conditions, Liebherr engineers have placed the cab of the R 996 successor back on the left side, standardising with other excavators in the range. The operator’s seat has been positioned as far left as possible in order to provide the best operator visibility of the attachment and working area. Ambient and low-level LED-lights make working at night easier and safer. The operator station is user-friendly and equipped with modern touch screen displays. The air conditioning system for the cabin is a modular design concept which is easily exchanged as a rotable component, as single or dual air conditioning systems are available.To further enhance the operator comfort, vacuum cleaner, premium cooled seats, HEPA filtration system and much more features are available.
The R 9600 offers a superior machine perimeter visibility system comprising of four cameras at strategic locations on the rotating uppercarriage. The dedicated monitor inside the cabin provides continuous 270° vision around the machine.
Assistance Systems and on-board controls
Setting new standards in the mining industry, the R 9600 is equipped with the Liebherr Assistance Systems. These advanced on-board applications are designed to support the operators in becoming more efficient through analytics and actionable insights from live data.
The Truck Loading Assistant helps the operator attain optimal productivity and efficiency. With 99% measurement accuracy, the system measures the instantaneous bucket payload and provides real-time information to the operator. The Truck Loading Assistant strategizes the number of passes required to achieve the target payload of the truck, and also provides a progressive update in achieving the strategy.
In addition, to provide operators and customers with productivity KPIs of the machine performance, the severity of the application and the operational conformance of the machine is realized in real-time on the machine.
The first Liebherr hydraulic excavator (HEX) Automation Product introduced to the Mining Industry is the Bucket Filling Assistant, an adaptive or semi-autonomous digging product which is available as an option for the backhoe version of machines.
It allows for easier and faster bucket filling with a consistent bucket fill factor, load after load even in the toughest digging conditions. As a result the overall productivity improves while the operator's fatigue level is reduced.
Designed for safe 24/7 operation and maintenance
Liebherr product development is centered around protecting the customer’s most important assets. The R 9600 was designed with respect to global safety standards for operators and maintenance personnel, ensuring that safety remains a top priority at all times.
The uppercarriage of the R 9600 has been designed to allow for quick and easy maintenance activities, and is accessible via a hydraulically controlled ergonomic 45° stairway. Enlarged walkways with handrails and non-slip perforated steps allow for safe and convenient inspections and maintenance at all levels of the machine, including engine and powertrain components. All major parts have been designed and positioned to allow easy access and quicker maintenance.
The central service flap provides fluid and lubricant access to all components and systems, which reduces potential downtimes. Component and system refill and drain points of the R 9600 are accessible from ground level with quick couplings and depressurizing valves.
R 9600 continues to write the success story
The R 9600 builds on two strong models of the Liebherr mining excavator portfolio: the R 996B and the R 9800. The first R 996 was introduced in 1995, followed by the R 996B in 2000. This very popular machine has been the benchmark in the mining market for the past 25 years, especially in Australia, where over 70% of these excavators have or are operating today accumulating 5.5 million machine hours.
The R 9600 is not only further building on the success of its predecessor but is also inspired by its big brother, the popular 800-tonne R 9800 sharing a long list of components that have been proven on the R 9800 over the past ten years.
As with all Liebherr mining equipment, the predecessor models R 996 and R 996B will continue to be supported with remanufacturing, repair and customer support services for the duration of the machine’s lifetime.
For more information on the new R 9600, visit the Liebherr website: www.liebherr.com/nextgeneration