Prefer to listen to (or along with) this piece? Now you can!
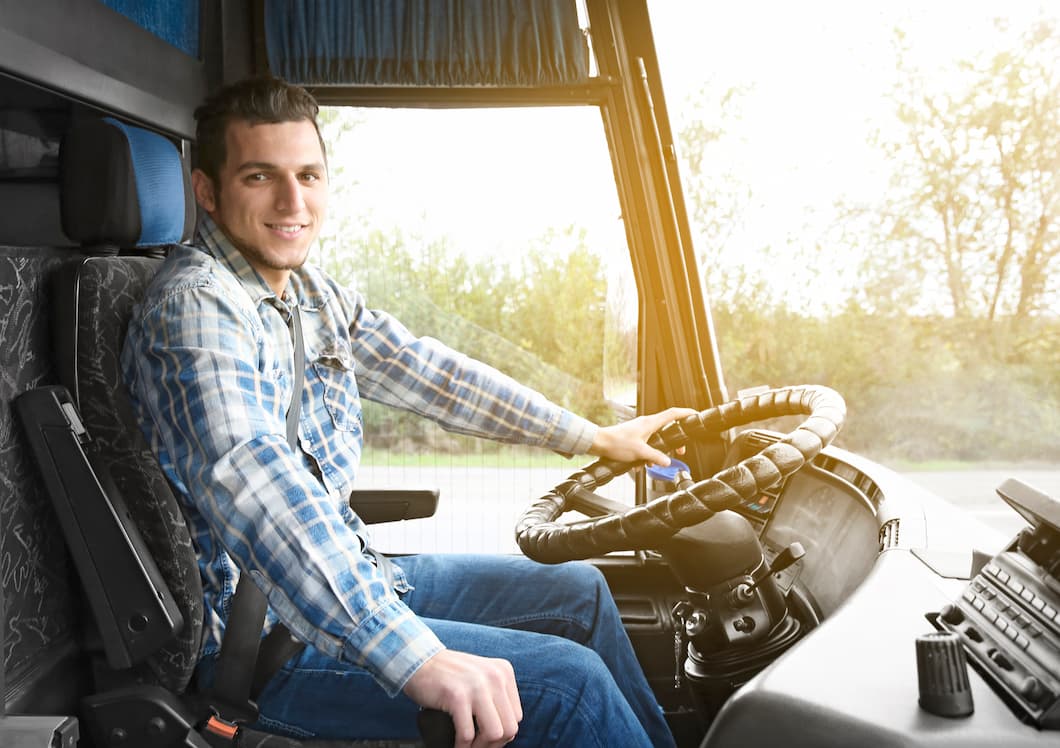
Baseball mitts, blue jeans, and new boots aren’t the only things that work best after a break-in period. Your truck’s new diesel engine needs a break-in period as well. And just like your jeans and mitt, there are right ways and wrong ways to break in your truck’s engine. In this piece, we’re going to look at:
Disclaimer:
Before we get started, it is important to consult your engine manufacturer's or mechanic’s specific instructions for breaking in your particular diesel engine. The following information is a summary of diesel engine break-in procedures.
Despite the latest innovations in engineering technology, engine makers have yet to design and produce an engine that does not require a break-in period. In a way, the break-in period is the final step in a diesel engine’s assembly process—utilizing the heat and pressure to ensure that the engine components are seated properly, much like warming up and stretching before intense physical activity.
During a diesel engine break-in process, the vehicle is purposefully heavily loaded and may be driven on hillier terrain to create maximum heat and pressure just short of overheating or abuse. This increased workload serves two functions—
- (a) to heat the components to allow for the best “mating” or fit within the engine
- (b) to produce a necessary amount of wear on certain parts that enable them to work more efficiently with each other
If a diesel engine is not properly “broken in” at the beginning of its operating life, various engine components will not properly mate, seat, or wear in such a way that allows for its optimal performance. The result of a failure to break in an engine range from a negative impact to fuel and oil economy, a potentially shortened engine life, increased diesel blow-by (gas leaking into the crankcase), and various other issues.
Skipping a break-in period for a diesel engine is especially troublesome for piston rings and their relation to the cylinder wall. As air pushes against the top and rear side of a piston ring, this will force the piston ring against the cylinder wall and cause an important level of wear. If an insufficient load on the piston is applied to a diesel engine during the break-in process, the piston ring and cylinder wall won’t wear properly against one another. This can result in cylinder glazing, crosshatch damage, and premature cylinder wear—possibly causing increased oil consumption and blow-by.
To properly break in a new or rebuilt diesel engine, the following steps should be taken within the first few minutes of the first startup.
Start the engine and immediately check it for leaks, excessive or unusual sounds (knocking, squeaking, and the like), or warning lights on the dashboard.These checks should occur quickly and only to ensure the safe driving of the vehicle.
Immediately after the truck appears free of issues and the engine is adequately warm, it should be driven at medium-to-high RPMs at peak torque (with a full load) without overheating the engine.
Before the first oil change of a new or rebuilt engine, diesel engines should not be left to idle for extended periods of time or run lighter loads with higher RPMs. It’s best to run the engines with the heaviest loads possible—always with a trailer—with varying RPMs short of abuse.
The break-in period for a diesel engine can vary depending on the engine size and style of driving. The recommended break-in period in which increased loading is applied to a diesel engine is around 150 hours. After this amount of time and use, operators should notice certain engine performance gains—including increased miles-per-gallon and smoother running. For larger semi trucks, this break-in period may be longer.
The break-in mileage for a diesel engine depends on a number of factors—including engine size, style of driving, and load size. A decent average for breaking in a new or rebuilt diesel engine, however, is somewhere between 500 and 1,000 miles for an initial break-in. Continued performance improvements can be observed even much further into the life of the engine— from 50,000 miles or even 100,000 miles.
The first oil change on a new diesel engine should happen sooner than following oil changes—at around 5,000 miles for a highway truck instead of the usual 10,000 miles. The reason for this is the increased level of metal debris present in the oil as a result of the engine break-in process—which may potentially fill up your oil filter more than usual. Following that first oil change, your usual 10,000-12,000 mile range is typically acceptable going forward.
Always check with the manufacturer of a new truck or with the mechanic who rebuilt the diesel engine for specific instructions on what type of oil or additives to use when breaking in a new diesel engine. However, if you’re using a standard roller valve train design diesel engine, no special “break-in oil” is likely necessary.
Because the break-in period for a diesel engine is ongoing, the process is a shared responsibility. A manufacturer or repair shop may perform an initial break-in on a Dyno machine. Repair shops will likely load up semi trucks with trailers during test drives. Preferably, a customer of an engine rebuild should leave a loaded trailer with the mechanic so they have one ready to go to assist in the break-in process. Because the initial stages of breaking in a diesel engine may last well past the first oil change, a customer or operator should be fully aware of the responsibilities inherent in the process to ensure a long working life for the engine.
To help make your commercial truck purchasing experience is as easy as possible, your friends at My Little Salesman are excited to connect you with hundreds of commercial truck dealers and individual sellers all over the United States and beyond.
Find Your Next Commercial Truck For Sale Today