“What are the costs associated with buying heavy equipment?”
When deciding upon what heavy equipment you can afford, the initial purchase price of the equipment is only the tip of the iceberg. Behind that upfront cost is a wide variety of associated costs for buying, keeping, and using said equipment.
Contents of this Guide
Let’s take a look at what costs you can expect—starting with the largest one.
As you look through heavy equipment listings, the sticker price for each piece of equipment is likely what stands out to you the most. And this is for a good reason—the list price will likely determine the affordability of said equipment. But other costs will hinge on this price, making it worthy of such attention.
Through most of this guide, we’re going to be using an average price of a piece of heavy equipment of $150,000.
But the initial purchase is just the beginning!

Unless you have the funds to buy heavy equipment outright, there’s a good chance that you will be financing the purchase. Though this seems like a given, even just a few interest percentage points higher or lower can result in a difference of tens of thousands of dollars by the end of the financing term. For this reason, it is important to not only look for the best heavy equipment financing options available to you but also to keep your credit rating in good standing with lenders.
So, how much would financing add to the purchase?
Working from an average equipment cost of $150,000 and an average interest rate is about 6%, the cost to finance this piece of equipment would be around $44,000.
Your heavy equipment is a major investment. To protect your investment and remain in compliance with lenders, you’ll need to insure your equipment. Depending on the lender and kind of equipment, you will need insurance that covers liability, property damage, and equipment breakdowns. And while warranties can fill in a portion of the coverage—such as breakdowns—they can also be expensive or not fulfill a lender’s need for coverage.
So, how much will it cost to insure a piece of heavy equipment over the span of a financing period (when such coverage is usually required)?
If the average cost of a piece of heavy equipment is $150,000 and carries an insurance coverage limit of $1 million with an average insurance rate of 1% of equipment value, the cost of insurance over a 5-year span would cost around $7,500. Keep in mind this figure does not include insuring the equipment after the fact.
Unlike buying a street-legal vehicle or a permanent structure, heavy equipment is only effective if it can be taken to where it is used. Most models of heavy equipment will require specialized transportation and personnel—including trucks, trailers, workers, and drivers. And the larger and heavier the equipment, the higher transportation costs will be anytime the equipment needs to be used. If you don’t already have access to the necessary personnel and equipment needed to transport your equipment, you will need to obtain said equipment.
So, on average, how much would it cost every year to transport equipment to its destination?
Due to the variation in size and use frequency of heavy equipment, it would cost over $50,000 to transport one item of equipment every year. This factor is determined by multiplying the average mileage traveled (just around 10,000 miles per year) by the average cost of $5 per mile. The actual rate would likely far surpass this, as it doesn’t take tolls, truck hiring, or various permits into consideration.
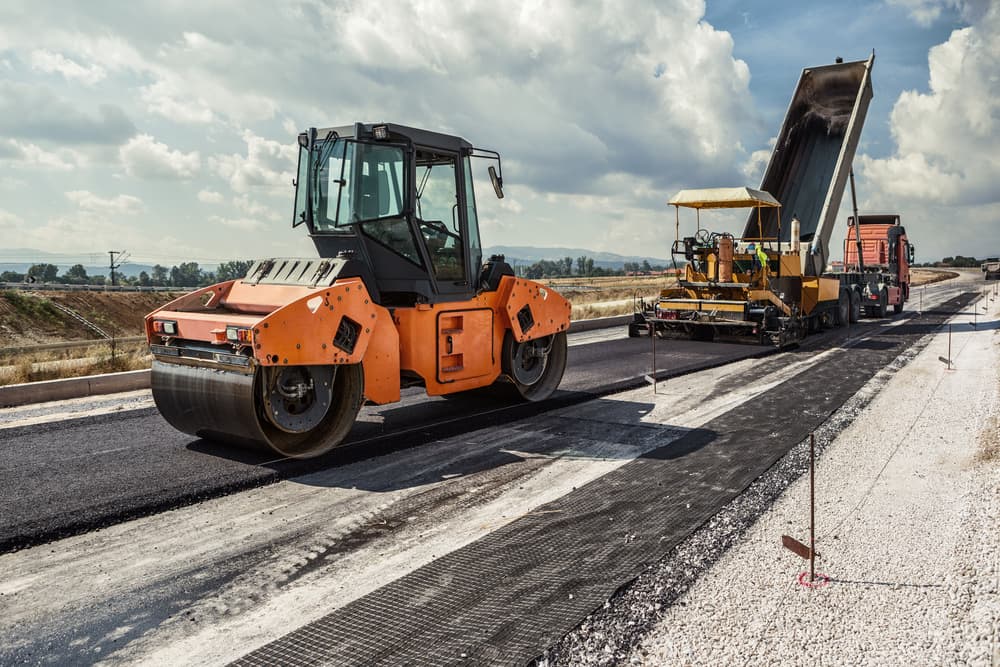
Heavy equipment will eventually wear out or break—that’s just a fact of life. And few breakdowns are cheap. When shopping for new heavy equipment models, you will need to keep in mind the cost to fix and maintain their components. You’ll likely need to set aside a monthly budget for said repairs, maintenance, and replacements. Having an equipment failure without adequate funds to fix it can leave you in the hole—metaphorically or physically, depending on the equipment.
So, how much would maintenance and repair cost per year for the average piece of heavy equipment?
A decent rule of thumb when it comes to maintenance and repair costs for heavy equipment is to budget about 10% of the cost of the equipment. With that being said, for a piece of heavy equipment costing $150,000, maintenance and repair would run very roughly about $15,000 a year.
For a piece of heavy equipment to begin to make money, it needs someone to operate it and fuel to power it. To make the most of a piece of heavy equipment, a full-time equipment operator will likely be necessary—meaning an entire full-time salary, preferably with benefits. Even after hiring someone, the fuel for heavy equipment to perform is also not cheap. Depending on the equipment's size and usage, fuel costs can easily run many thousands of dollars per month.
What is the average monthly cost of operation and fuel for heavy equipment?
To employ a full-time heavy equipment operator will cost between $6,000-$8,000—a figure that considers income, taxes, benefits, and the like. This price will vary widely depending on the equipment that needs to be used, any possible overtime, additional overheads, and the like.
To fuel a piece of heavy equipment for a month, if diesel prices sit at around $4.10 per gallon (as they were at the time of this publishing), the monthly rate would average around $3,300.
For such an expensive investment, you’ll want to protect it with secure storage while it is not being used. This is a place that is accessible, large, accommodating, and secure—not only keeping equipment safe from the elements but also from theft and vandalism. Storage facilities should also be insured and comply with storage regulations for said equipment.
So, what is the average cost to securely store heavy equipment?
The various sizes, requirements, and styles of storage make it difficult to determine an average price for secure heavy equipment storage. However, considering lots as well as warehouses and garages, the average monthly cost for secure equipment storage is somewhere between $500 and $1,000.
When purchasing any equipment, it is important to remember the taxes and registration fees that will be required. And these can vary greatly. Fortunately, registration costs for heavy equipment are reasonable.
Depending on where you intend to buy your heavy equipment in the United States and its intended purpose, sales tax rates can vary. For instance, farm equipment in Missouri is tax-exempt but construction equipment is not. For this reason, it is important to consult a tax professional familiar with your state’s guidelines to make sure you’re compliant with local tax codes.
So, how much do sales taxes on heavy equipment cost in the United States?
As mentioned above, tax rates and conditions vary depending on the equipment’s use and the state where it is purchased. Sales tax rates for non-exempt heavy equipment purchases can be as little as 4% or as much as over 10%. This means that, for a model of heavy equipment costing $150,000, the taxes can range from $6,000 to $15,000 or more.
In Conclusion, Plan to Spend!
As you know, running heavy equipment isn’t cheap! But proper budgeting, understanding of costs, and eliminating surprises can all go a long way towards building revenue.
Find the heavy equipment you need—in seconds!
To make the heavy equipment shopping process as easy as possible, you owe it to yourself to dive into the listing from mylittlesalesman.com. Compare literally hundreds of thousands of listings. Find precisely what you need within your budget with easy-to-use search filters. It couldn’t be any more simple!
Find your heavy equipment now from My Little Salesman.